THE 'ULTIMATE' WAREHOUSE FLOOR SOLUTION
Published on 14 April 2021
In June 2018, Colin Shephard wrote an article for Concrete Magazine about Twintec's involvement in a recent pile-supported floor slab for a major international supermarket chain. Since then, two additional projects for the same retail client (with a third one to construct later this year) have been completed. Here, he discusses the latest developments in this process.
The Twintec ULTIMATE solution focuses on using a hybrid reinforcement of high-performance steel fibres and proprietary steel fabric to create effectively 'seamless' slabs. This, together with a specially adapted and carefully controlled concrete mix design and highly skilled and experienced installation teams, allows very large slab areas to be constructed very quickly and with no opening movement joints. Designs are undertaken using finite-element analysis tools (most notably DIANA non-linear FEA software) to a predefined maximum design crack width.
The result is slabs that provide total flexibility to the end-user for racking and process equipment installation and which have significantly reduced maintenance requirements and better long-term control of flatness criteria. Where the end-user is also the building owner, it is easy to demonstrate that this approach makes good financial sense as the life-time savings significantly outweigh the slightly increased initial cost.
Peterborough project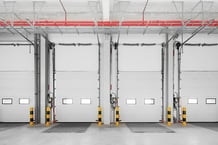
For the client though, additional constraints existed that needed to be considered carefully. Due to historic issues, steel-fibre reinforcement was not acceptable. Movement joints were considered desirable at key locations due to varying temperate zones within the building and additional movement joints were required along the dock leveller locations due to the design of the precast dock structure.
Reinforcement
First then, steel fibres. The client had experienced a significant issue on a project in mainland Europe where fibres were used by an inexperienced contractor, at the wrong dosage, and incorporated into concrete that was over two hours old at the time of integration. All of this had led to a significant failure in the floor slab which, while patently not related to the suitability of steel fibres, had led to a blanket rejection of fibres for subsequent projects. As such, the only option was to adopt a two-layer fabric system. On the plus side, this provides for easier installation of in-floor heating conduits as they can be fixed to the bottom reinforcement. On the downside, it makes the installation process more labour intensive and can limit the daily output (circa 1600m2 per day was constructed using this system).
Thermal differences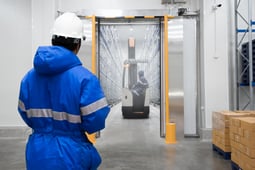
The second consideration was the presence of movement joints in the slab because of having different ambient internal temperature zones. Due to the type of product stored in the facility, the internal slabs are subject to a variety of different temperatures from -25°C, through 4-14°C and general ambient temperature. The zones where a specific temperature is maintained are regulated by means of either chillers (with insulated slabs under) or using heated slabs (with cast-in floor heating circuits). The zones are separated from each other by either insulated panel walls built off foundation slabs (for the -25°C areas), or by insulated panel walls built off the slab (in all other areas).
Thus, for the areas where the slabs are between 4 and 14°C, the temperature differential is significant enough to affect the shrinkage and a movement joint is incorporated to reduce the likelihood of stress-related cracking. In this case, the joints are generally located just adjacent to the internal wall locations and these are then covered by concrete kerbs installed to protect the panel walls from impact damage.
In the location of access doors between different temperature zones the CoSinus joint system (manufactured by Hengelhoef Concrete Joints) was installed to allow maximum possible joint opening but with a joint edge that would not be subject to impact shock from the transition of MHE. Maximum long-term shrinkage movement (over the whole-life span of the building) was calculated to check that these would not become an issue to the client over time. The joint in the doorways into the freezer slab (-25°C area) consists of a double run of joint designed to allow the installation of in-slab electric heater grids with a physical break from the main chilled and frozen slabs.
Shrinkage and restraint
Finally then, the treatment at the dock-leveller interface. The ULTIMATE system normally allows for the removal of the armoured joint that is, so often, incorporated just in front of the dock levellers – an area where arguably the most aggressive traffic will be present as goods are loaded in and out of the delivery wagons via the dock levellers. This degree of aggressive wear across the joint in this location has long been an area of concern and the ability of the ULTIMATE design to remove this is a major benefit.
However, to do this the design of the dock structure needs to be capable of dealing with the additional forces generated at the base of the back wall from the slab ‘pulling’ slightly and create sufficient restraint to this to hold the slab in place. Because, particularly in the UK, precast dock structures are specified that do not provide a sufficiently robust connection at this location, the movement joint has had to be kept in the slab. This then means consideration of the long-term potential shrinkage at this location and an estimation of how much opening the slab could be expected at this location over the 50-year lifespan of the building. If this is deemed excessive then additional measures are necessary to mitigate the opening.
In-floor heating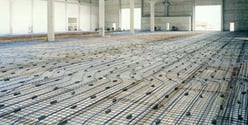
Another benefit of this form of construction over traditional ‘jointed’ or even ‘jointless’ solutions is realised when considering the inter-relation between the joint layout and the in-floor heating zones. In-floor heating can be laid effectively to a maximum length of pipe fed from a single manifold position. This, together with the required spacing of pipes to deliver the correct degree of temperature control, defines how many ‘pipe coils’ are required in the building.
Unfortunately, it is not always possible or appropriate to place the coils of pipework under movement joint locations within the slab. This means, often, that the number of coils that need to be placed (and hence the number of manifold positions that need to be accommodated within the building) are ‘defined’ by the slab panel sizes and shapes. With the ULTIMATE solution it is possible to design the panel size around the heating coil length, thus reducing wastage in the system design and allowing fewer manifold positions to be formed. This helps to free up floorspace for the end-user for racking and marshalling zones. On a recent project this resulted in a reduction of over 55% in manifold positions within the building.
Racking and flatness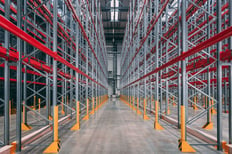
Similarly, with the racking layout, the position of the tied construction breaks within the ULTIMATE slab can easily be adjusted to suit the client’s racking layout – removing any breaks from within the racking zones – and, as an added benefit, allowing specialist flattening and rectifying techniques to proceed more efficiently. This enables better control of surface level and flatness than is possible with normal jointed or jointless slab construction. Movement joints within VNA racking are always an area where issues are experienced with the slab flatness and the removal of all joints, including formed, tied, construction breaks, provides a significant benefit to the end-user in terms of long-term operability of the slab.
Consideration
All of this consideration and design development has been fed into the latest project for the client and will result in the construction of a largely seamless, traditionally reinforced, concrete slab that performs optimally for the lifespan of the building with little or no maintenance requirement.
Speak to the specialists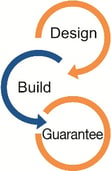
Twintec offers the personalised solution you need for your warehouse, logistics facility or factory concrete floor slab. Design-Build-Guarantee.
Talk to the concrete floor slab experts about your next project mail@twintec.co.uk or 01788 567722.
Download Colin Shephard's editorial from Concrete Magazine here
Topics: Twintec Ultimate
Comments
If you liked this article please share it or add a comment below