Twintec UK Completes New Lidl Distribution Centre
Published on 29 January 2018
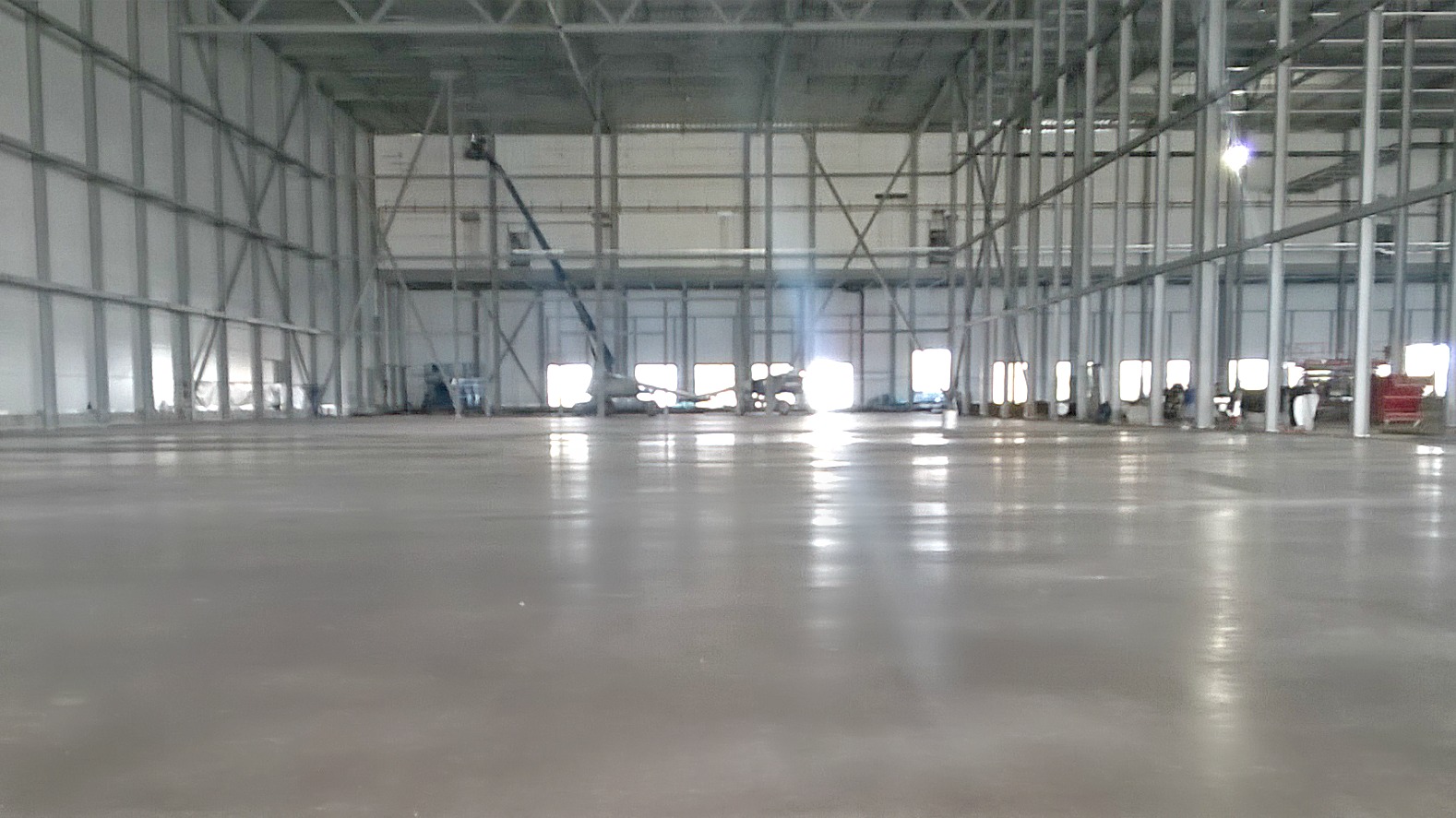
Twintec has completed the design and construction of 58,000m2 of floor slabs for a new regional distribution centre on Central Park, Avonmouth for Lidl as part of their ongoing expansion in the UK market. Central Park is a 600 acre warehouse and distribution park development strategically located within the region and designed to be the South West's largest distribution park.
Lidl’s international specification for distribution centres imposed a number of requirements not usually seen in the UK market and Twintec’s international experience was key to fulfilling these. Working closely with the main contractor, TSL Projects Ltd, and our design consultant, DIANA FEA BV, we developed designs for the various loading categories required by the client. Unusually for Twintec, the slabs were required to be reinforced traditionally rather than utilising steel fibres, however the client also wanted the benefits of jointless panels. To achieve this, we used NLFEA design methods to produce designs in standard steel bar reinforcement to cater for the loads and to limit shrinkage cracking on the surface of the slabs. This technology is the same as that employed in the Twintec ULTIMATE® product but in this instance the client insisted upon traditional movement joints around panels.
The distribution centre had a number of different zones. The freezer slab consisted of a 250mm thick structural slab with glycol pipework system embedded, 240mm of approved insulation (by others) and a 240mm thick SFRC wearing slab. The main warehouse was divided into high bay and low bay areas, the majority of which included underfloor heating pipework cast in the slab. Different load requirements applied in these areas and we designed three different slab depths (230mm, 240mm and 250mm) to suit these. In addition to the ground floor areas we also constructed slabs on profile metal decking to office and plant room areas.
To reduce wheel impact damage and provide a smooth transition in areas of greatest use by MHE, Twintec and the client team defined specific locations where a sinus-wave profile joint was used in lieu of standard steel armoured construction joints. The sinus profile at the joint crossing effectively reduced impact damage at the opening to zero.
Due to the high demand in the area for concrete, an on-site batching plant was supplied by Rockland Concrete. We worked closely with Rockland to develop the correct concrete mix.
Under the Twintec Design-Build-Guarantee package, total responsibility is taken for the floor slab including design, materials, construction and specialised equipment, together with providing a 12 year warranty.
Contact our UK business team mail@twintec.co.uk for more information.
Topics: Twintec Ultimate, Warehouse
Comments
If you liked this article please share it or add a comment below